How to Choose the Right Threaded Flange for Your Project: A Comprehensive Guide
Release time:
2025-03-28
How to Choose the Right Threaded Flange for Your Project Understanding Threaded Flanges: An Overview Threaded flanges are essential components in various piping systems, providing reliable connections between pipes and equipment. Their unique design allows for easy installation and removal, making them a popular choice in many industrial and construction applications. In this section, we will expl
How to Choose the Right Threaded Flange for Your Project
Understanding Threaded Flanges: An Overview
Threaded flanges are essential components in various piping systems, providing reliable connections between pipes and equipment. Their unique design allows for easy installation and removal, making them a popular choice in many industrial and construction applications. In this section, we will explore the fundamental aspects of threaded flanges, including their definitions and common uses.
What Are Threaded Flanges?
Threaded flanges are circular pieces of metal with a hole in the center that allows for the attachment of pipes, valves, or other fittings. The inner surface of the flange features threads that enable the flange to be screwed onto corresponding threads on the pipe or fitting. This design provides a secure connection while allowing for easy disassembly when needed.
Common Uses of Threaded Flanges
Threaded flanges are widely used in various industries, including oil and gas, water treatment, HVAC systems, and chemical processing. They are particularly useful in applications where frequent disassembly is required, as they can be easily tightened or loosened without the need for welding.
Types of Threaded Flanges
When choosing the right threaded flange for your project, it's essential to understand the different types available. Each type has unique characteristics that make it suitable for specific applications.
1. Slip-On Threaded Flanges
Slip-on threaded flanges are designed to slide over the pipe before being welded in place. They provide a larger surface area for welding, making them suitable for applications requiring additional strength.
2. Weld Neck Threaded Flanges
Weld neck threaded flanges have a long, tapered neck that provides a strong connection between the flange and the pipe. This design reduces stress concentration, making it ideal for high-pressure applications.
3. Blind Threaded Flanges
Blind threaded flanges are solid discs used to seal the end of a piping system. They are often used in situations where future access may be needed, allowing for easy removal when necessary.
4. Socket Weld Threaded Flanges
Socket weld threaded flanges are designed for use with socket-welded pipes. They offer a strong connection and are commonly used in high-pressure applications where leak prevention is crucial.
Material Selection for Threaded Flanges
Choosing the right material for your threaded flanges is critical to ensure durability and performance. The material must withstand the specific conditions of your project, including temperature, pressure, and the nature of the fluid being transported.
1. Carbon Steel Flanges
Carbon steel flanges are popular due to their strength and affordability. They are suitable for low to medium-pressure applications but may corrode in harsh environments.
2. Stainless Steel Flanges
Stainless steel flanges offer excellent corrosion resistance, making them ideal for applications involving chemicals or high humidity. They are available in various grades, each suitable for different environments.
3. Alloy Steel Flanges
Alloy steel flanges provide enhanced strength and resistance to wear and high temperatures. They are often used in demanding applications, such as oil and gas extraction.
4. Plastic Flanges
Plastic flanges are lightweight and resistant to corrosion, making them suitable for specific applications where metal flanges may not be appropriate. They are often used in water treatment and chemical processing.
Flange Sizing and Standards
Proper sizing is crucial when selecting threaded flanges to ensure a secure and leak-free connection. Flanges are available in various sizes and are often produced according to specific industry standards.
1. Flange Size Measurement
Flange sizes are typically measured by their nominal pipe size (NPS) and pressure class. The NPS indicates the diameter of the pipe, while the pressure class indicates the maximum pressure the flange can withstand.
2. Industry Standards for Flanges
Several organizations establish standards for threaded flanges, including the American National Standards Institute (ANSI), American Society of Mechanical Engineers (ASME), and the International Organization for Standardization (ISO). Familiarizing yourself with these standards is essential to ensure compatibility with existing systems.
Installation Tips for Threaded Flanges
Proper installation of threaded flanges is vital for achieving a secure and leak-free connection. The following tips can help ensure a successful installation process.
1. Preparing the Flange and Pipe
Before installation, clean the threaded surfaces of both the flange and the pipe to remove any debris or contaminants. This will help ensure a tight seal during assembly.
2. Using the Correct Thread Sealant
Choose an appropriate thread sealant for your specific application. Teflon tape and pipe dope are common options that can provide added sealing capabilities.
3. Tightening the Flange
When tightening the flange, use a torque wrench to ensure that the bolts are tightened to the manufacturer's specifications. Over-tightening can lead to damage, while under-tightening can result in leaks.
4. Inspecting the Connection
After installation, inspect the connection for signs of leaks. Conduct a pressure test if necessary to ensure the integrity of the joint.
Common Problems and Solutions
Even with careful selection and installation, issues can still arise with threaded flanges. Understanding these common problems and their solutions can help you address them effectively.
1. Leaks
Leaks are one of the most common issues associated with threaded flanges. They can result from improper installation, inadequate sealing, or damaged threads. To resolve leaks, check the tightness of the connection and replace any damaged components.
2. Corrosion
Corrosion can occur due to exposure to harsh environments or incompatible materials. To prevent corrosion, select flanges made from appropriate materials and apply protective coatings if necessary.
3. Thread Damage
Damaged threads can compromise the integrity of the connection. Inspect threads regularly and replace any components with signs of wear or damage.
Frequently Asked Questions (FAQs)
1. What is the difference between threaded flanges and welded flanges?
Threaded flanges are screwed onto pipes, allowing for easy installation and removal, while welded flanges are permanently attached through welding, providing a more robust connection.
2. Can I use a threaded flange in high-pressure applications?
Yes, but it is essential to select a flange specifically designed for high-pressure applications, such as weld neck or alloy steel flanges.
3. How do I know which material is best for my threaded flange?
Consider the environment in which the flange will be used, including temperature, pressure, and exposure to corrosive substances, to determine the most suitable material.
4. Are there standards I need to follow for flange selection?
Yes, familiarize yourself with industry standards like ANSI, ASME, and ISO to ensure compatibility and safety in your piping system.
5. How can I prevent leaks in threaded flange connections?
Ensure proper installation techniques, use appropriate thread sealants, and regularly inspect and maintain the flange connections to prevent leaks.
Conclusion
Choosing the right threaded flange for your project is crucial for ensuring the efficiency, safety, and longevity of your piping system. By understanding the various types, materials, sizing, and installation techniques, you can make informed decisions that will benefit your project in the long run. Proper selection and maintenance will lead to a reliable and leak-free connection, ultimately contributing to the success of your construction or industrial endeavors.
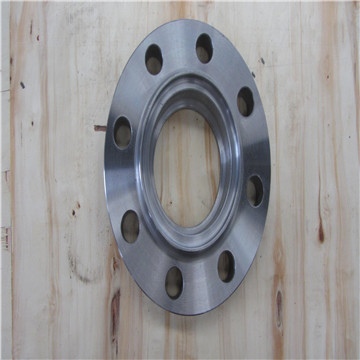
Latest developments
The Advantages of Using Flat Flanges in Architectural Design Table of Contents Introduction to Flat Flanges in Architecture Understanding Flat Flanges: Definition and Types Benefits of Using Flat Flanges in Architecture Enhancing Structural Integrity with Flat Flanges Design Flexibility and Aesthetic Appeal Cost-Effectiveness of Flat Flanges in Projects Applications of Flat Flan
Understanding Steel Industries Forgings: A Key Component in Construction and Decorative Materials
Forgings in the steel industry are a fundamental production technique that involves shaping metal through localized compressive forces. This process results in components that exhibit enhanced strength, durability, and resistance to fatigue compared to those produced through other methods, such as casting or machining. In the context of construction and decorative materials, steel forgings play a
Why Forging of Stainless Steel is Essential for Modern Industry
Why Forging of Stainless Steel is Essential for Modern Industry Table of Contents 1. Introduction to Stainless Steel Forging 2. Importance of Forging in Stainless Steel Production 3. The Forging Process: A Detailed Overview 4. Benefits of Forging Stainless Steel 5. Key Applications of Forged Stainless Steel 6. Innovations in Stainless Steel Forging 7. Environmental Imp
Understanding Non-Standard Flanges: An Essential Guide for Construction and Decorative Materials
Non-standard flanges, as the name suggests, are flanges that do not conform to widely recognized industry standards. While standard flanges are manufactured to meet specific dimensions, pressure ratings, and material compositions defined by organizations like ASME, ISO, or ANSI, non-standard flanges offer flexibility to cater to unique project requirements. This can include variations in size, sha
How Japanese Standard Flanges Boost Your Pipeline Efficiency: A Comprehensive Guide
How Japanese Standard Flanges Enhance Your Pipeline Efficiency Introduction to Pipeline Efficiency and Flanges In the world of industrial piping systems, **pipeline efficiency** is paramount. The integrity and performance of a piping system can greatly influence operational costs, safety, and productivity. **Flanges** play a crucial role in this efficiency, serving as a connection point between di
Understanding American Standard Flanges: Essential Insights for Construction Professionals
American standard flanges are critical components in piping systems, commonly used in construction and various industrial applications. These flanges serve as connection points for pipes, valves, and other equipment, ensuring a secure and leak-proof assembly. Understanding the specifications and applications of American standard flanges is essential for construction professionals involved in the d