Why Forging of Stainless Steel is Essential for Modern Industry
Release time:
2025-04-01
Why Forging of Stainless Steel is Essential for Modern Industry Table of Contents 1. Introduction to Stainless Steel Forging 2. Importance of Forging in Stainless Steel Production 3. The Forging Process: A Detailed Overview 4. Benefits of Forging Stainless Steel 5. Key Applications of Forged Stainless Steel 6. Innovations in Stainless Steel Forging 7. Environmental Imp
Why Forging of Stainless Steel is Essential for Modern Industry
Table of Contents
- 1. Introduction to Stainless Steel Forging
- 2. Importance of Forging in Stainless Steel Production
- 3. The Forging Process: A Detailed Overview
- 4. Benefits of Forging Stainless Steel
- 5. Key Applications of Forged Stainless Steel
- 6. Innovations in Stainless Steel Forging
- 7. Environmental Impact of Forging Stainless Steel
- 8. The Future of Stainless Steel Forging
- 9. Frequently Asked Questions
- 10. Conclusion
1. Introduction to Stainless Steel Forging
Forging is a time-honored process that has stood the test of time in manufacturing, especially when it comes to stainless steel. This technique involves shaping metal using compressive forces, which can be applied through various methods such as hammering or pressing. In modern industry, the forging of stainless steel has gained prominence due to its superior mechanical properties, making it a go-to choice for critical applications that demand strength, durability, and corrosion resistance.
2. Importance of Forging in Stainless Steel Production
Stainless steel forging plays a crucial role in the overall production and performance of stainless steel components. The process enhances the physical properties of the metal, resulting in parts that exhibit higher strength and resistance to wear and tear. Unlike other manufacturing methods, such as casting, forging ensures that the grain structure of the steel is refined, providing additional toughness and impact resistance.
Furthermore, the ability to produce complex shapes through forging allows industries to meet specific design requirements without compromising on quality. This is particularly important in sectors such as aerospace, automotive, and oil and gas, where the integrity of components can have serious safety implications.
3. The Forging Process: A Detailed Overview
The forging process can generally be broken down into several key stages:
3.1 Heating
The stainless steel is heated to a temperature that makes it malleable but not molten. This temperature typically ranges between 1,100°C to 1,200°C, depending on the specific alloy composition.
3.2 Forming
Once heated, the metal is shaped using various tools, including hammers, presses, or dies. There are different types of forging processes, including:
- Open Die Forging: The metal is shaped between flat surfaces, allowing for flexibility in design.
- Closed Die Forging: The metal is confined within a die, which provides greater precision for complex shapes.
- Upset Forging: This method increases the diameter of the workpiece by compressing it in a specific direction.
3.3 Cooling
After forming, the forged stainless steel component is allowed to cool. This can be done naturally or through controlled means to achieve desired mechanical properties.
3.4 Finishing
Finally, the component may undergo additional processes such as machining, heat treatment, or surface finishing to meet the required specifications.
4. Benefits of Forging Stainless Steel
Forging stainless steel offers numerous advantages that are vital to modern industries:
4.1 Enhanced Strength and Durability
Forged stainless steel components are typically stronger than their cast counterparts. The forging process refines the grain structure, resulting in a denser and more resilient material.
4.2 Superior Corrosion Resistance
Stainless steel inherently possesses resistance to corrosion, and the forging process enhances this property further. This makes forged stainless steel ideal for environments exposed to moisture, chemicals, and extreme temperatures.
4.3 Cost-Effectiveness
Although the initial costs of forging can be higher than other methods, the long-term benefits, such as reduced maintenance and replacement costs, often outweigh the initial investment.
4.4 Design Flexibility
Forging offers a high degree of design flexibility, allowing for the production of complex shapes that would be difficult or impossible to achieve with other methods.
4.5 Reduced Waste
The forging process typically produces less scrap metal than processes like casting, making it a more environmentally friendly option.
5. Key Applications of Forged Stainless Steel
Forged stainless steel is utilized across various industries due to its robust nature and adaptability:
5.1 Aerospace Industry
In the aerospace sector, forged stainless steel components play a critical role in ensuring the safety and efficiency of aircraft. Components such as landing gear, engine mounts, and structural frames require the strength and reliability offered by forged stainless steel.
5.2 Automotive Industry
The automotive industry relies on forged stainless steel for critical components such as crankshafts, connecting rods, and suspension parts. These components must withstand high levels of stress and strain, making forging an ideal manufacturing process.
5.3 Oil and Gas Sector
The oil and gas industry demands materials that can withstand extreme conditions. Forged stainless steel is used in valves, pumps, and pipelines, where resistance to corrosion and high pressure is essential.
5.4 Medical Devices
In the medical field, forged stainless steel is often found in surgical instruments and implants. The material's non-reactive properties and strength make it suitable for use in critical applications where patient safety is paramount.
5.5 Construction and Infrastructure
Forged stainless steel is also commonly used in construction, particularly for structural components such as beams and fasteners. Its durability ensures the longevity and safety of buildings and infrastructure.
6. Innovations in Stainless Steel Forging
The forging industry has embraced technological advancements that improve efficiency and precision. Innovations such as:
6.1 Computer Numerical Control (CNC)
CNC technology allows for precise control over the forging process, reducing human error and ensuring consistent quality.
6.2 Advanced Materials
Research into new stainless steel alloys continues to enhance the properties of forged components, such as increased strength and improved corrosion resistance.
6.3 Automation
Automated forging processes increase production efficiency and reduce labor costs, making forged stainless steel components more accessible to various industries.
7. Environmental Impact of Forging Stainless Steel
As industries move towards sustainability, the environmental impact of manufacturing processes is under scrutiny. Forging stainless steel presents several environmental benefits:
7.1 Energy Efficiency
The forging process generally requires less energy than other methods like casting, contributing to lower greenhouse gas emissions.
7.2 Recycling
Stainless steel is highly recyclable, and the forging process utilizes recycled materials effectively, reducing the demand for virgin resources.
7.3 Reduced Waste Production
As mentioned earlier, forging produces less waste than other methods, contributing to a more sustainable manufacturing cycle.
8. The Future of Stainless Steel Forging
The future of stainless steel forging looks promising as industries continue to prioritize quality and sustainability. With ongoing research and innovation, we can expect:
8.1 Increased Automation
As automation technologies evolve, the forging process will become even more efficient, allowing for faster production times and reduced costs.
8.2 Smart Manufacturing
The integration of IoT and smart technologies will lead to real-time monitoring and predictive maintenance, enhancing the quality and reliability of forged products.
8.3 Sustainable Practices
With an increasing focus on reducing the carbon footprint, the forging industry will likely adopt more sustainable practices and materials.
9. Frequently Asked Questions
9.1 What is the difference between forging and casting?
Forging involves shaping metal using compressive forces, while casting involves pouring molten metal into a mold. Forged components are generally stronger and have better mechanical properties than cast ones.
9.2 Why is stainless steel preferred for forging?
Stainless steel is preferred for its excellent corrosion resistance, strength, and durability, making it suitable for a wide range of industrial applications.
9.3 What industries benefit from forged stainless steel?
Industries such as aerospace, automotive, oil and gas, medical devices, and construction benefit significantly from forged stainless steel components.
9.4 How does the forging process affect the properties of stainless steel?
The forging process refines the grain structure of stainless steel, resulting in enhanced strength, toughness, and resistance to wear and corrosion.
9.5 Is forged stainless steel more expensive than other types of stainless steel?
While the initial costs of forging can be higher, the long-term benefits such as durability and reduced maintenance often justify the investment.
10. Conclusion
The forging of stainless steel is not just a manufacturing process; it is a vital component of modern industry. Its ability to produce strong, durable, and corrosion-resistant materials makes it essential for a myriad of applications across various sectors. As technology continues to advance, the future of stainless steel forging promises to be even more innovative and sustainable, further solidifying its importance in meeting the demands of our ever-evolving industrial landscape.
In summary, embracing the forging process for stainless steel components ensures that industries are equipped with the highest quality materials, ready to tackle the challenges of today and tomorrow.
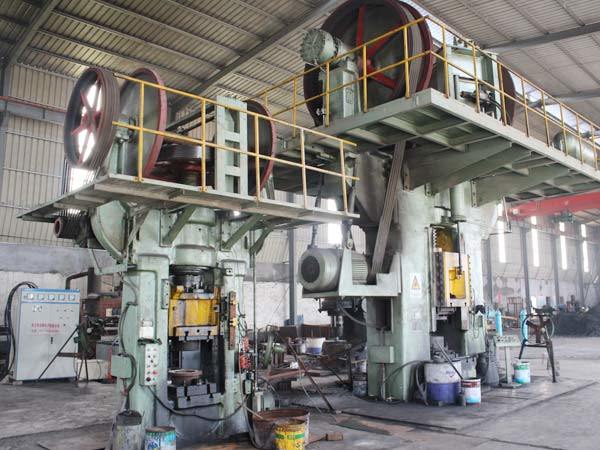
Latest developments
The Advantages of Using Flat Flanges in Architectural Design Table of Contents Introduction to Flat Flanges in Architecture Understanding Flat Flanges: Definition and Types Benefits of Using Flat Flanges in Architecture Enhancing Structural Integrity with Flat Flanges Design Flexibility and Aesthetic Appeal Cost-Effectiveness of Flat Flanges in Projects Applications of Flat Flan
Understanding Steel Industries Forgings: A Key Component in Construction and Decorative Materials
Forgings in the steel industry are a fundamental production technique that involves shaping metal through localized compressive forces. This process results in components that exhibit enhanced strength, durability, and resistance to fatigue compared to those produced through other methods, such as casting or machining. In the context of construction and decorative materials, steel forgings play a
Why Forging of Stainless Steel is Essential for Modern Industry
Why Forging of Stainless Steel is Essential for Modern Industry Table of Contents 1. Introduction to Stainless Steel Forging 2. Importance of Forging in Stainless Steel Production 3. The Forging Process: A Detailed Overview 4. Benefits of Forging Stainless Steel 5. Key Applications of Forged Stainless Steel 6. Innovations in Stainless Steel Forging 7. Environmental Imp
Understanding Non-Standard Flanges: An Essential Guide for Construction and Decorative Materials
Non-standard flanges, as the name suggests, are flanges that do not conform to widely recognized industry standards. While standard flanges are manufactured to meet specific dimensions, pressure ratings, and material compositions defined by organizations like ASME, ISO, or ANSI, non-standard flanges offer flexibility to cater to unique project requirements. This can include variations in size, sha
How Japanese Standard Flanges Boost Your Pipeline Efficiency: A Comprehensive Guide
How Japanese Standard Flanges Enhance Your Pipeline Efficiency Introduction to Pipeline Efficiency and Flanges In the world of industrial piping systems, **pipeline efficiency** is paramount. The integrity and performance of a piping system can greatly influence operational costs, safety, and productivity. **Flanges** play a crucial role in this efficiency, serving as a connection point between di
Understanding American Standard Flanges: Essential Insights for Construction Professionals
American standard flanges are critical components in piping systems, commonly used in construction and various industrial applications. These flanges serve as connection points for pipes, valves, and other equipment, ensuring a secure and leak-proof assembly. Understanding the specifications and applications of American standard flanges is essential for construction professionals involved in the d