Exploring Different Types of Threaded Flanges for Various Applications
Release time:
2025-05-07
Exploring Different Types of Threaded Flanges for Various Applications Table of Contents 1. Introduction to Threaded Flanges 2. Importance of Threaded Flanges in Construction 3. Types of Threaded Flanges and Their Applications 3.1 Standard Threaded Flanges 3.2 Slip-On Threaded Flanges 3.3 Blind Threaded Flanges 3.4 Socket Weld Threaded Flanges
Exploring Different Types of Threaded Flanges for Various Applications
Table of Contents
- 1. Introduction to Threaded Flanges
- 2. Importance of Threaded Flanges in Construction
- 3. Types of Threaded Flanges and Their Applications
- 3.1 Standard Threaded Flanges
- 3.2 Slip-On Threaded Flanges
- 3.3 Blind Threaded Flanges
- 3.4 Socket Weld Threaded Flanges
- 3.5 Weld Neck Threaded Flanges
- 4. Material Types for Threaded Flanges
- 5. Installation Techniques and Best Practices
- 6. Maintenance and Inspection of Threaded Flanges
- 7. Common Misconceptions about Threaded Flanges
- 8. Conclusion
- 9. Frequently Asked Questions
1. Introduction to Threaded Flanges
Threaded flanges are essential components in the piping and construction industries. They serve as connection points that allow for the easy assembly and disassembly of piping systems. Unlike their welded counterparts, threaded flanges use a male and female thread interface, enabling straightforward installation and removal without the need for welding equipment. This flexibility is particularly advantageous in environments where maintenance is frequent or where welding isn't feasible.
2. Importance of Threaded Flanges in Construction
In construction and piping applications, the choice of flanges can significantly impact the efficiency and safety of a system. Threaded flanges provide several advantages, including ease of installation, versatility in application, and the ability to withstand various pressures and temperatures. They are widely used in industries such as oil and gas, water treatment, and chemical manufacturing, where reliability and durability are paramount.
3. Types of Threaded Flanges and Their Applications
Understanding the different types of threaded flanges is crucial for selecting the appropriate flange for a specific application. Below, we explore several common types:
3.1 Standard Threaded Flanges
Standard threaded flanges, often referred to as "screw flanges," are typically used in low-pressure applications. They feature a straightforward design, allowing for easy assembly with standard piping. These flanges are ideal for applications where pressure isn't a major concern, such as in water distribution systems.
3.2 Slip-On Threaded Flanges
Slip-on threaded flanges are designed to slip over the pipe and then be welded in place. This design makes them easier to align and install compared to welded flanges. They are frequently used in low-pressure systems and can be easily removed or replaced, enhancing their utility in maintenance-heavy environments.
3.3 Blind Threaded Flanges
Blind threaded flanges are solid flanges that do not have any internal threading. They serve as a closure for piping systems and are ideal for applications requiring temporary or permanent closure points. Their robust construction allows them to withstand significant pressure, making them suitable for high-pressure systems.
3.4 Socket Weld Threaded Flanges
Socket weld threaded flanges are designed to fit into a recess in the flange, providing a strong and secure joint. This design enhances the strength and durability of the connection, making socket weld flanges ideal for high-pressure and high-temperature applications, particularly in the oil and gas industry.
3.5 Weld Neck Threaded Flanges
Weld neck threaded flanges have a long neck that allows for a smooth transition between the flange and the pipe. This design minimizes stress concentrations and is ideal for high-pressure applications. They are commonly used in critical service applications where reliability is essential.
4. Material Types for Threaded Flanges
The material selection for threaded flanges plays a crucial role in their performance and longevity. Here are some of the common materials used:
- **Carbon Steel**: Known for its strength and durability, carbon steel flanges are widely used in low to medium-pressure applications. They are cost-effective but may require protective coatings to prevent corrosion.
- **Stainless Steel**: Renowned for its corrosion resistance, stainless steel flanges are suitable for various environments, including those exposed to chemicals and high humidity.
- **Alloy Steel**: Alloy steel flanges offer enhanced strength and resistance to high temperatures, making them suitable for demanding applications like power generation or petrochemicals.
- **Plastic and Composite Materials**: In applications where corrosion resistance is critical, plastic and composite flanges can be an excellent choice, offering lightweight solutions without compromising on strength.
5. Installation Techniques and Best Practices
The installation of threaded flanges requires careful attention to detail to ensure a secure and leak-free connection. Here are the best practices to follow:
- **Cleaning Threads**: Before installation, ensure that the threads on both the pipe and the flange are clean and free of debris, rust, or other contaminants.
- **Use of Thread Sealants**: Applying a suitable thread sealant can enhance the seal and prevent leaks, particularly in applications involving liquids or gases.
- **Proper Torque**: Use a torque wrench to apply the appropriate torque to the flange bolts. Over-tightening can lead to failure, while under-tightening can result in leaks.
- **Alignment**: Ensure that the pipes and flanges are properly aligned before tightening to prevent stress on the system and ensure a long-lasting connection.
6. Maintenance and Inspection of Threaded Flanges
Regular maintenance and inspection are crucial to ensuring the longevity and reliability of threaded flanges. Here are key considerations:
- **Visual Inspections**: Regularly inspect flanges for signs of wear, corrosion, or leaks. Early detection can prevent costly repairs and downtime.
- **Pressure Testing**: Conduct pressure tests periodically to ensure the integrity of the flanges and the overall piping system.
- **Retightening**: In some cases, due to thermal expansion or vibration, flange connections may require retightening. Monitor connections closely, especially in high-vibration environments.
7. Common Misconceptions about Threaded Flanges
Several misconceptions can lead to improper usage of threaded flanges. Here are a few myths debunked:
- **Myth 1: All Flanges are the Same**: Different applications and environments necessitate the use of specific types of flanges, each with its own design and material considerations.
- **Myth 2: Threaded Flanges are Weak**: While some may perceive threaded connections as less robust than welded ones, when properly installed, they can be equally reliable and strong.
- **Myth 3: Maintenance Isn't Necessary**: Regular inspections and maintenance are vital for ensuring the safety and longevity of threaded flanges and the overall piping system.
8. Conclusion
Threaded flanges play a pivotal role in the construction and piping industries, providing versatile solutions for connecting pipes securely. By understanding the various types of threaded flanges, their applications, and best practices for installation and maintenance, professionals can make informed decisions that enhance the safety and efficiency of their projects. As industries continue to evolve, the demand for durable and reliable flanges remains constant, underscoring their importance in modern construction.
9. Frequently Asked Questions
What are the advantages of using threaded flanges?
Threaded flanges offer ease of installation and removal, making them ideal for maintenance-heavy environments. They also provide a reliable seal when properly torqued.
Can threaded flanges be used in high-pressure applications?
Yes, certain types of threaded flanges, such as socket weld and weld neck flanges, are specifically designed for high-pressure applications.
How do I choose the right material for my threaded flanges?
The choice of material depends on the application's environment, pressure, and temperature. Stainless steel is ideal for corrosive environments, while carbon steel is suitable for lower pressure applications.
What is the best way to maintain threaded flanges?
Regular visual inspections, pressure testing, and monitoring for leaks are essential maintenance practices for threaded flanges.
Are threaded flanges interchangeable with welded flanges?
While both threaded and welded flanges serve similar functions, they are not interchangeable. Selecting the appropriate flange type depends on the application requirements.
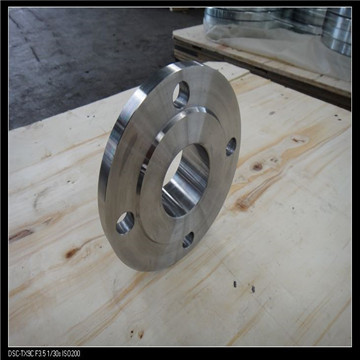
Latest developments
Innovations in the Forging of Stainless Steel for Superior Performance
Innovations in the Forging of Stainless Steel for Superior Performance Table of Contents 1. Introduction to Stainless Steel Forging Innovations 2. Importance of Stainless Steel in Various Industries 3. Overview of the Forging Process 4. Technological Advancements in Stainless Steel Forging 4.1. Machine Automation and Robotics 4.2.
Understanding Non-Standard Flanges: Importance and Applications in Construction
Non-standard flanges are critical components in piping systems, particularly within the construction and decorative materials sectors. Unlike standard flanges, which adhere to established dimensions and specifications, non-standard flanges are tailored to meet unique requirements that can vary based on specific project needs, environmental factors, or design specifications. This adaptability makes
Exploring the Versatility of Japanese Standard Flanges in Various Applications
Exploring the Versatility of Japanese Standard Flanges in Various Applications Table of Contents 1. Introduction to Japanese Standard Flanges 2. What Are Flanges? 2.1 Types of Flanges 3. Understanding Japanese Standard Flanges 3.1 Design and Specifications 4. Applications of Japanese Standard Flanges
--- Flanges are critical components in piping systems, serving as a connection point between pipes, valves, pumps, and other equipment. The term "American standard flange" refers to a specific category of flanges designed according to established standards in the United States, predominantly including ANSI (American National Standards Institute) and ASME (American Society of Mechanical Engineers)
Exploring Different Types of Threaded Flanges for Various Applications
Exploring Different Types of Threaded Flanges for Various Applications Table of Contents 1. Introduction to Threaded Flanges 2. Importance of Threaded Flanges in Construction 3. Types of Threaded Flanges and Their Applications 3.1 Standard Threaded Flanges 3.2 Slip-On Threaded Flanges 3.3 Blind Threaded Flanges 3.4 Socket Weld Threaded Flanges
The Essential Guide to Flanged Connections in Construction and Decorative Materials
Flanged connections are a critical component in the construction and decorative materials industry, particularly when dealing with piping systems. These connections consist of two flanges, which are flat pieces of metal or plastic with symmetrical holes that allow them to be bolted together. This design provides a reliable and robust means of connecting pipes, valves, fittings, and other equipment