Innovations in the Forging of Stainless Steel for Superior Performance
Release time:
2025-05-11
Innovations in the Forging of Stainless Steel for Superior Performance Table of Contents 1. Introduction to Stainless Steel Forging Innovations 2. Importance of Stainless Steel in Various Industries 3. Overview of the Forging Process 4. Technological Advancements in Stainless Steel Forging 4.1. Machine Automation and Robotics 4.2.
Innovations in the Forging of Stainless Steel for Superior Performance
Table of Contents
- 1. Introduction to Stainless Steel Forging Innovations
- 2. Importance of Stainless Steel in Various Industries
- 3. Overview of the Forging Process
- 4. Technological Advancements in Stainless Steel Forging
- 4.1. Machine Automation and Robotics
- 4.2. Enhanced Heat Treatment Techniques
- 4.3. Innovative Materials and Alloys
- 5. Performance Improvements Through Modern Forging
- 6. Sustainability in Stainless Steel Forging
- 7. Future Trends in Stainless Steel Forging
- 8. Frequently Asked Questions
- 9. Conclusion
1. Introduction to Stainless Steel Forging Innovations
The forging of stainless steel has undergone significant transformations over the years, driven by the need for **enhanced performance** and **durability** in diverse applications. As industries evolve, so too does the technology and methodology behind stainless steel forging. This article delves into the latest **innovations** that are redefining standards and pushing the boundaries of what forged stainless steel can achieve.
2. Importance of Stainless Steel in Various Industries
Stainless steel is a critical material in industries such as construction, automotive, aerospace, and medical devices. Its **corrosion resistance**, **strength**, and **aesthetic appeal** make it an ideal choice for a wide range of applications. With the rise in technological advancement and innovation, the demand for high-performance stainless steel products continues to surge. Understanding the significance of these innovations is vital for industry stakeholders aiming to leverage stainless steel's potential.
3. Overview of the Forging Process
Forging is a manufacturing process that shapes metal using compressive forces. When it comes to stainless steel, forging can enhance its mechanical properties and performance characteristics. The process typically involves several stages:
1. **Heating**: The stainless steel is heated to a temperature where it becomes malleable, usually between 1,100°C and 1,300°C.
2. **Deformation**: The heated metal is then shaped through various techniques, such as open-die forging, closed-die forging, and ring rolling.
3. **Cooling**: After shaping, the forged piece is cooled, often through controlled methods to achieve desired properties.
4. **Finishing**: The final step may include surface treatments, machining, or heat treatment to ensure optimal performance.
Each stage of the forging process is essential for maximizing the qualities of the stainless steel used.
4. Technological Advancements in Stainless Steel Forging
As technology advances, the forging of stainless steel has seen remarkable innovations that enhance both efficiency and performance.
4.1. Machine Automation and Robotics
The integration of **machine automation** and **robotics** in the forging process has revolutionized production. Automated systems not only improve precision but also significantly reduce lead times and labor costs. For instance, robotic arms can handle heavy components safely and efficiently, leading to fewer workplace injuries and improved productivity.
4.2. Enhanced Heat Treatment Techniques
Modern **heat treatment techniques** are tailored to maximize the properties of stainless steel. **Techniques like quenching and tempering** have become more sophisticated, allowing for better control over the final properties of the forged steel. Innovations such as **vacuum heat treatment** ensure a cleaner process, reducing contamination and enhancing the mechanical properties of the final product.
4.3. Innovative Materials and Alloys
The development of new **alloys and materials** has allowed for the creation of stainless steel that exhibits improved strength and corrosion resistance. Innovations such as martensitic stainless steels offer enhanced hardness and wear resistance, making them perfect for demanding applications. The exploration of **advanced compositions** also leads to lighter and stronger materials, contributing to overall performance enhancements.
5. Performance Improvements Through Modern Forging
The innovations in the forging process directly translate to performance improvements in stainless steel products. These advancements lead to:
1. **Increased Strength and Durability**: Enhanced forging techniques ensure that the molecular structure of the steel is optimized, resulting in superior tensile strength and resistance to wear.
2. **Improved Corrosion Resistance**: Modern alloys provide enhanced resistance to environmental factors, making stainless steel suitable for harsher conditions.
3. **Better Fabrication and Machinability**: Innovations allow for the production of stainless steel that is easier to machine and fabricate, which is essential for complex components.
4. **Cost Efficiency**: By maximizing material properties and streamlining production processes, industries can reduce waste and lower costs.
The impact of these performance improvements is profound, driving growth and innovation across sectors.
6. Sustainability in Stainless Steel Forging
Sustainability has become a focal point in manufacturing processes. The forging of stainless steel is no exception. Innovations in this area are leading to more environmentally friendly practices, such as:
- **Recycling and Reuse of Materials**: The use of recycled stainless steel not only reduces raw material costs but also minimizes the environmental footprint.
- **Energy Efficient Processes**: Techniques that reduce energy consumption during the forging process are being adopted, contributing to lower overall emissions.
- **Eco-friendly Treatments**: Development of non-toxic surface treatments ensures that harmful substances are not released into the environment.
By embracing sustainability, industries can meet regulatory requirements while also appealing to environmentally conscious consumers.
7. Future Trends in Stainless Steel Forging
Looking ahead, several trends are poised to shape the future of stainless steel forging:
1. **Smart Manufacturing**: The adoption of IoT (Internet of Things) devices will enable real-time monitoring and optimization of the forging process, enhancing efficiency and reducing downtime.
2. **3D Printing and Additive Manufacturing**: Although traditionally not associated with forging, advancements in **3D printing** may complement forging methods, allowing for the rapid prototyping of complex shapes.
3. **Customized Solutions**: As industries become more specialized, there will be an increasing demand for customized stainless steel solutions tailored to specific needs.
These trends highlight the dynamic nature of the industry and the ongoing drive toward innovation and excellence.
8. Frequently Asked Questions
What is stainless steel forging?
Stainless steel forging is a manufacturing process that involves shaping stainless steel using compressive forces, which enhances its mechanical properties and overall performance.
How does automation improve the stainless steel forging process?
Automation enhances precision, reduces labor costs, and increases production speed. It also minimizes human error and improves safety in the workplace.
What are the benefits of modern heat treatment techniques?
Modern heat treatment techniques improve the strength, toughness, and corrosion resistance of forged stainless steel, ensuring better performance in various applications.
Are there sustainable practices in stainless steel forging?
Yes, sustainable practices include recycling materials, adopting energy-efficient processes, and using eco-friendly surface treatments to minimize environmental impact.
What future advancements can we expect in stainless steel forging?
Future advancements may include smart manufacturing technologies, integration with additive manufacturing, and more customized solutions for specific industry needs.
9. Conclusion
The forging of stainless steel is witnessing transformative innovations that enhance its performance across various industries. From automation and advanced heat treatment techniques to sustainable practices and future trends, the landscape of stainless steel forging is evolving rapidly. As these innovations continue to unfold, they promise not only to improve the quality of products but also to drive sustainability and efficiency in manufacturing processes. Embracing these advancements will be crucial for industries looking to maintain a competitive edge in an ever-changing market.
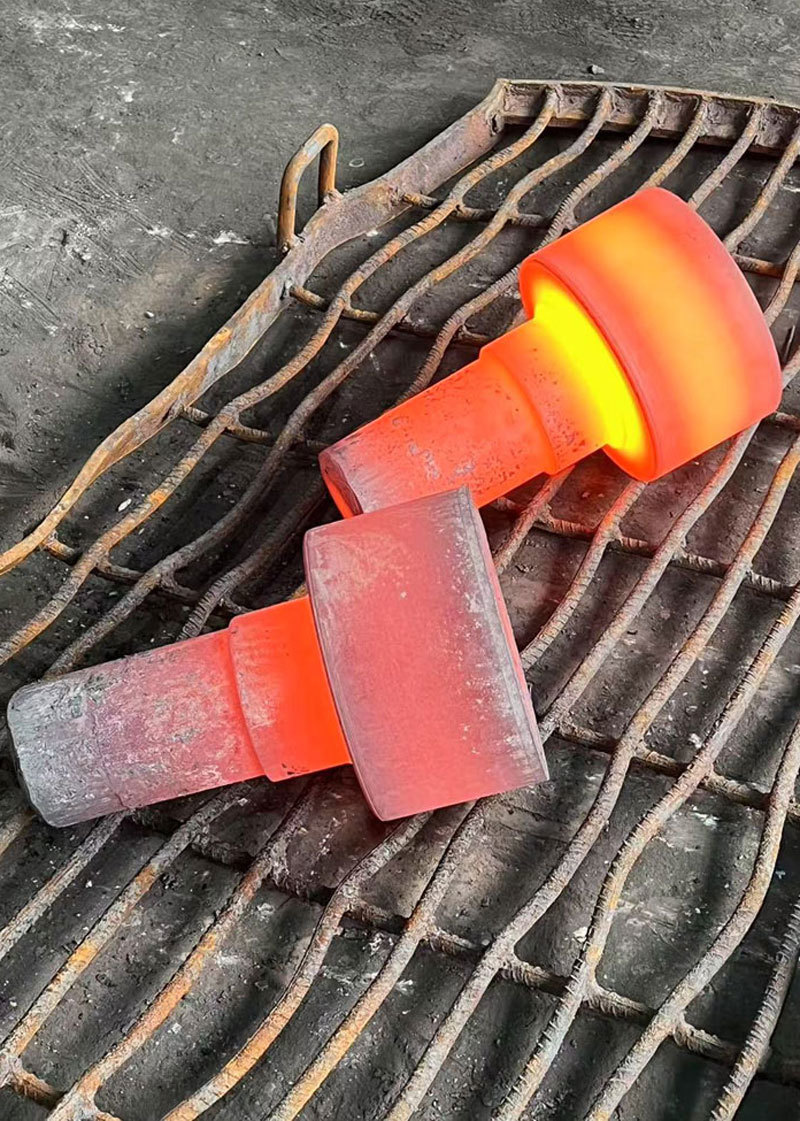
Previous
Latest developments
Innovations in the Forging of Stainless Steel for Superior Performance
Innovations in the Forging of Stainless Steel for Superior Performance Table of Contents 1. Introduction to Stainless Steel Forging Innovations 2. Importance of Stainless Steel in Various Industries 3. Overview of the Forging Process 4. Technological Advancements in Stainless Steel Forging 4.1. Machine Automation and Robotics 4.2.
Understanding Non-Standard Flanges: Importance and Applications in Construction
Non-standard flanges are critical components in piping systems, particularly within the construction and decorative materials sectors. Unlike standard flanges, which adhere to established dimensions and specifications, non-standard flanges are tailored to meet unique requirements that can vary based on specific project needs, environmental factors, or design specifications. This adaptability makes
Exploring the Versatility of Japanese Standard Flanges in Various Applications
Exploring the Versatility of Japanese Standard Flanges in Various Applications Table of Contents 1. Introduction to Japanese Standard Flanges 2. What Are Flanges? 2.1 Types of Flanges 3. Understanding Japanese Standard Flanges 3.1 Design and Specifications 4. Applications of Japanese Standard Flanges
--- Flanges are critical components in piping systems, serving as a connection point between pipes, valves, pumps, and other equipment. The term "American standard flange" refers to a specific category of flanges designed according to established standards in the United States, predominantly including ANSI (American National Standards Institute) and ASME (American Society of Mechanical Engineers)
Exploring Different Types of Threaded Flanges for Various Applications
Exploring Different Types of Threaded Flanges for Various Applications Table of Contents 1. Introduction to Threaded Flanges 2. Importance of Threaded Flanges in Construction 3. Types of Threaded Flanges and Their Applications 3.1 Standard Threaded Flanges 3.2 Slip-On Threaded Flanges 3.3 Blind Threaded Flanges 3.4 Socket Weld Threaded Flanges
The Essential Guide to Flanged Connections in Construction and Decorative Materials
Flanged connections are a critical component in the construction and decorative materials industry, particularly when dealing with piping systems. These connections consist of two flanges, which are flat pieces of metal or plastic with symmetrical holes that allow them to be bolted together. This design provides a reliable and robust means of connecting pipes, valves, fittings, and other equipment