Flat Flanges vs. Other Flange Types: Which is Best for You?
Release time:
2025-05-13
Flat Flanges vs. Other Flange Types: Which is Best for You? When it comes to the world of construction and decorative materials, understanding the nuances of flange types is crucial for making informed decisions. Among these, flat flanges stand out for their unique characteristics and applications. In this extensive article, we will delve deep into the world of flat flanges, comparing them to othe
Flat Flanges vs. Other Flange Types: Which is Best for You?
When it comes to the world of construction and decorative materials, understanding the nuances of flange types is crucial for making informed decisions. Among these, flat flanges stand out for their unique characteristics and applications. In this extensive article, we will delve deep into the world of flat flanges, comparing them to other flange types and helping you decide which option is best suited for your specific needs.
Table of Contents
- 1. Introduction to Flange Types
- 2. Understanding Flat Flanges
- 3. Exploring Other Flange Types
- 4. Advantages of Flat Flanges
- 5. Disadvantages of Flat Flanges
- 6. Advantages of Other Flange Types
- 7. Disadvantages of Other Flange Types
- 8. How to Choose the Right Flange Type
- 9. Frequently Asked Questions
- 10. Conclusion
1. Introduction to Flange Types
Flanges are crucial components in various piping systems, providing a means to connect pipes, valves, pumps, and other equipment. They allow for easy access for cleaning, inspection, and modification. While there are numerous flange types available, flat flanges are among the most commonly used. Understanding the features and functions of each flange type is essential for selecting the most appropriate one for your project.
2. Understanding Flat Flanges
Flat flanges, also known as slip-on flanges, are characterized by their flat surface, which allows them to slide over the pipe before being welded in place. This design makes them relatively easy to install, which is one reason they are favored in many applications. Flat flanges are typically made from materials such as carbon steel, stainless steel, or alloy steel, ensuring durability and strength.
2.1 Specifications of Flat Flanges
Flat flanges come in various sizes and pressure classes. It's essential to select the right specifications to ensure compatibility with the pipes they will connect. Common standards include ANSI, ASME, and DIN, which define dimensions, tolerances, and materials used in manufacturing flat flanges.
3. Exploring Other Flange Types
While flat flanges are popular, several other flange types serve specific purposes in piping systems. Understanding these alternatives will help you in making a more informed decision.
3.1 Weld Neck Flanges
Weld neck flanges feature a long tapered neck, which is welded to the pipe for a strong connection. This design makes them ideal for high-pressure applications, as they are less prone to stress concentration.
3.2 Blind Flanges
Blind flanges are solid flanges used to seal the end of a piping system. They are useful for maintenance purposes, allowing for easy access to remove or replace portions of the system without needing a complete shutdown.
3.3 Socket Weld Flanges
Socket weld flanges have a socket into which the pipe is inserted before welding. This connection type is often used for small-diameter pipes and is advantageous in high-pressure applications.
4. Advantages of Flat Flanges
Flat flanges offer several advantages that make them a popular choice in various applications:
- Ease of Installation: The simple design allows for quick installation and alignment.
- Cost-Effective: Generally less expensive than other types, flat flanges can be a budget-friendly option.
- Versatility: They can be used in a wide range of applications, from low-pressure systems to more complex setups.
- Availability: Flat flanges are widely available, making them easy to source for various projects.
5. Disadvantages of Flat Flanges
Despite their advantages, flat flanges also have some limitations:
- Pressure Limitations: Flat flanges are not typically suitable for high-pressure applications compared to other types.
- Leak Potential: If not properly installed, flat flanges can be prone to leaks.
6. Advantages of Other Flange Types
Each flange type comes with its own set of advantages, making them suitable for specific applications:
- Weld Neck Flanges: Excellent for high-pressure situations, providing enhanced strength.
- Blind Flanges: Offer a reliable seal for system maintenance and pressure testing.
- Socket Weld Flanges: Provide a strong and permanent connection in smaller pipe systems.
7. Disadvantages of Other Flange Types
While other flange types have their benefits, they also come with drawbacks:
- Complex Installation: Some types, such as weld neck flanges, require skilled labor for installation.
- Higher Cost: Specialized flanges can be more expensive than flat flanges.
8. How to Choose the Right Flange Type
Choosing the right flange type for your project requires careful consideration of several factors:
- Application Requirements: Understand the pressure, temperature, and medium in the piping system.
- Installation Environment: Consider whether the installation area allows for easy access and whether it requires specialized tools.
- Budget Constraints: Assess the total cost of the flanges, including installation.
9. Frequently Asked Questions
9.1 What are the primary differences between flat flanges and weld neck flanges?
Flat flanges are simpler and easier to install, making them cost-effective for low-pressure systems, while weld neck flanges provide superior strength for high-pressure applications due to their design.
9.2 Are flat flanges suitable for high-temperature applications?
Flat flanges can handle moderate temperatures, but for high-temperature applications, it is recommended to use flanges specifically designed for such environments.
9.3 Can flat flanges be used for all pipe sizes?
Flat flanges are available in various sizes, but it is essential to select the appropriate size based on your specific piping system requirements.
9.4 How do I ensure a proper seal with flat flanges?
To ensure a proper seal, ensure that the flange surfaces are clean and free of debris. Additionally, using the correct gasket material and applying appropriate torque during installation is crucial.
9.5 What materials are flat flanges typically made from?
Flat flanges are commonly made from carbon steel, stainless steel, and alloy steel, providing durability for various applications.
10. Conclusion
In conclusion, selecting between flat flanges and other flange types hinges on understanding the specific requirements of your project. Flat flanges offer simplicity and cost-effectiveness for standard applications, while other types like weld neck and blind flanges excel in specialized situations. By carefully considering the advantages and disadvantages of each flange type, along with the specific needs of your piping system, you can make an informed decision that leads to efficient and reliable performance in your construction projects.
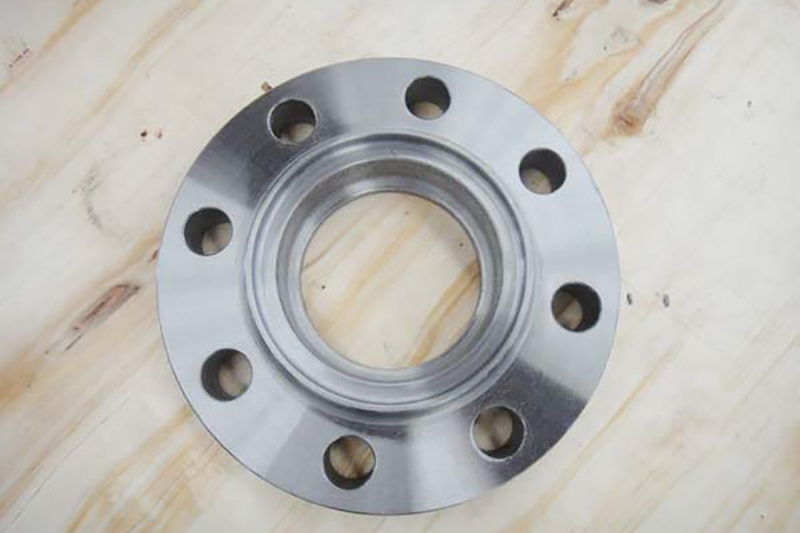
Latest developments
How to Choose the Right Japanese Standard Flanges for Your Project
How to Choose the Right Japanese Standard Flanges for Your Project When embarking on a construction project, selecting the appropriate components is crucial for ensuring the integrity and efficiency of your systems. Among these components, **Japanese standard flanges** hold significant importance, especially in piping systems. This guide provides a detailed exploration of how to choose the right f
Understanding American Standard Flanges: Essential Components in Construction
When it comes to the construction and plumbing industries, the term "American Standard flange" is often mentioned, yet many may not fully understand what it entails. A flange is a critical component used to connect pipes, valves, pumps, and other equipment, forming a robust, leak-proof joint. The American Standard flanges are designed in accordance with specific standards set forth by the American
The Role of Threaded Flanges in Enhancing Pipeline Integrity
The Role of Threaded Flanges in Enhancing Pipeline Integrity Table of Contents Introduction to Threaded Flanges What Are Threaded Flanges? The Importance of Threaded Flanges in Pipeline Systems Applications of Threaded Flanges Advantages of Using Threaded Flanges Design and Manufacturing of Threaded Flanges Installation and Maintenance Best Practices Frequently Ask
Understanding Flanged Connections: Essential Insights for Your Construction Projects
Flanged connections are vital components in various piping systems, especially in the construction and decorative materials sector. They play a critical role in ensuring the integrity and stability of piping connections, making them an essential consideration for engineers, architects, and builders alike. At its core, a flanged connection consists of two flat surfaces with matching holes, typicall
Durable Flanged Connection from China Manufacturers Enhances Pipeline Reliability
In refinery turnarounds and plant shutdowns, durable flanged connection from China manufacturers demonstrates its practical advantages. The ability to quickly disassemble and reassemble piping sections helps maintenance teams meet tight schedule windows, minimizing production losses during critical servicing periods.
Durable Axle-Type Forgings for Machinery from China Manufacturers Enhance Equipment Longevity
For OEMs seeking to improve equipment reliability, durable axle-type forgings for machinery from China manufacturers offer a proven solution. Their balanced combination of mechanical properties and production consistency makes them a practical choice for critical drivetrain components.