The Role of Threaded Flanges in Enhancing Pipeline Integrity
Release time:
2025-05-17
The Role of Threaded Flanges in Enhancing Pipeline Integrity Table of Contents Introduction to Threaded Flanges What Are Threaded Flanges? The Importance of Threaded Flanges in Pipeline Systems Applications of Threaded Flanges Advantages of Using Threaded Flanges Design and Manufacturing of Threaded Flanges Installation and Maintenance Best Practices Frequently Ask
The Role of Threaded Flanges in Enhancing Pipeline Integrity
Table of Contents
- Introduction to Threaded Flanges
- What Are Threaded Flanges?
- The Importance of Threaded Flanges in Pipeline Systems
- Applications of Threaded Flanges
- Advantages of Using Threaded Flanges
- Design and Manufacturing of Threaded Flanges
- Installation and Maintenance Best Practices
- Frequently Asked Questions (FAQs)
- Conclusion
Introduction to Threaded Flanges
Threaded flanges play a pivotal role in enhancing the integrity of pipeline systems. These essential components are widely used in various industries, including oil and gas, water supply, and chemical processing. By ensuring secure connections between pipes and fittings, threaded flanges contribute significantly to the overall reliability and safety of pipeline systems. Understanding their function, design, and applications is crucial for professionals involved in pipeline construction and maintenance.
What Are Threaded Flanges?
Threaded flanges are circular mechanical components designed to connect two different sections of a pipeline. Unlike standard flanges, which require welds for attachment, threaded flanges feature internal threads that enable them to screw onto the corresponding external threads of a pipe. This design allows for easy assembly and disassembly, making maintenance more straightforward.
The Design of Threaded Flanges
Threaded flanges come in various designs, including raised face, flat face, and ring-type joints. The most common material used for manufacturing these flanges is carbon steel, although they can also be found in stainless steel and other alloys, depending on the application requirements. The dimensions and pressure ratings of threaded flanges are standardized, ensuring compatibility across different systems.
The Importance of Threaded Flanges in Pipeline Systems
The importance of threaded flanges cannot be overstated. They provide a secure, leak-proof joint that is essential for maintaining the integrity of pipelines. In high-pressure applications, the need for reliable connections becomes even more critical, as any failure can result in hazardous leaks or catastrophic failures.
Ensuring Pipeline Safety
Threaded flanges contribute to pipeline safety by allowing for the quick replacement of damaged sections, reducing downtime and maintenance costs. Their ability to be easily removed and replaced means that inspection and servicing can occur without extensive modifications to the pipeline system.
Applications of Threaded Flanges
Threaded flanges are versatile components used across various industries, each with specific requirements and challenges.
Oil and Gas Industry
In the oil and gas sector, threaded flanges are employed in drilling rigs and refining processes. Their robust design ensures that they can withstand the high pressures and corrosive environments often encountered in these applications.
Water Supply Systems
Municipal water supply systems also utilize threaded flanges for connecting different piping sections. The ease of installation and maintenance makes them ideal for systems requiring regular servicing.
Chemical Processing
In chemical processing plants, threaded flanges are essential for handling hazardous materials. Their ability to provide a secure seal reduces the risk of leaks, which is vital for worker safety and environmental protection.
Advantages of Using Threaded Flanges
The benefits of using threaded flanges extend beyond simply connecting pipes. Here are some key advantages:
Easy Installation and Removal
Threaded flanges can be installed and removed without specialized equipment, allowing for quicker maintenance and repairs. This feature is particularly beneficial in environments where downtime must be minimized.
Cost-Effective
The use of threaded flanges can lead to significant cost savings. Their design reduces the need for welding, which can be labor-intensive and require skilled labor, thus lowering installation and maintenance costs.
Leak Prevention
The threaded design provides a secure connection that minimizes the risk of leaks. Properly installed threaded flanges create a tight seal that can withstand various pressures and temperatures.
Design and Manufacturing of Threaded Flanges
The design and manufacturing process of threaded flanges involves several critical steps to ensure quality and performance.
Material Selection
Selecting the right material is crucial, as the flange must withstand the operational environment. Carbon steel is commonly used, but materials like stainless steel or alloy steel may be necessary for more demanding applications.
Manufacturing Standards
Threaded flanges must adhere to industry standards such as ANSI, ASME, or ISO. These standards ensure consistency in dimensions, pressure ratings, and material properties.
Quality Control
Quality assurance is vital during manufacturing. Each flange is tested for dimensional accuracy, pressure rating, and material integrity to ensure it meets the specified requirements.
Installation and Maintenance Best Practices
Proper installation and maintenance of threaded flanges are key to ensuring pipeline integrity.
Installation Guidelines
1. **Surface Preparation**: Ensure that the mating surfaces are clean and free from debris.
2. **Torque Specifications**: Follow manufacturer torque specifications to avoid over-tightening, which can lead to flange failure.
3. **Sealant Usage**: Depending on the application, a suitable thread sealant may be applied to enhance the seal and prevent leaks.
Regular Maintenance
Conduct regular inspections to identify signs of wear or corrosion. Replace flanges that show signs of damage to maintain pipeline integrity. Keeping records of maintenance activities can help track performance over time.
Frequently Asked Questions (FAQs)
1. What is the difference between threaded and welded flanges?
Threaded flanges can be screwed onto pipes, allowing for easy disassembly, whereas welded flanges are permanently attached through welding.
2. Are threaded flanges suitable for high-pressure applications?
Yes, threaded flanges are designed to handle high-pressure situations, but it's essential to select the right material and pressure rating for the application.
3. How do I determine the correct size of a threaded flange?
The correct size can be determined by matching the flange to the pipe size and type, following industry standards for dimensions.
4. Can threaded flanges be used for all types of piping materials?
Threaded flanges are most commonly used with steel pipes, but they can also be utilized with other materials, provided the flange and pipe are compatible.
5. What maintenance is required for threaded flanges?
Regular inspections for wear, corrosion, and proper torque should be conducted, along with replacing damaged flanges as needed.
Conclusion
Threaded flanges are integral to enhancing pipeline integrity across various industries. Their unique design facilitates easy installation and maintenance, making them a preferred choice for many applications. By ensuring secure connections, they help prevent leaks and failures, contributing to the safety and reliability of pipeline systems. Understanding the importance, applications, and best practices associated with threaded flanges can significantly enhance the operational efficiency of any pipeline project. Embracing these components is not just a matter of choice but a necessity for maintaining the integrity and safety of modern piping systems.
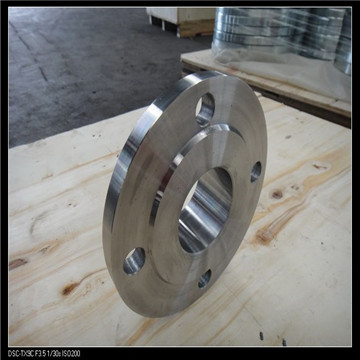
Latest developments
How to Choose the Right Japanese Standard Flanges for Your Project
How to Choose the Right Japanese Standard Flanges for Your Project When embarking on a construction project, selecting the appropriate components is crucial for ensuring the integrity and efficiency of your systems. Among these components, **Japanese standard flanges** hold significant importance, especially in piping systems. This guide provides a detailed exploration of how to choose the right f
Understanding American Standard Flanges: Essential Components in Construction
When it comes to the construction and plumbing industries, the term "American Standard flange" is often mentioned, yet many may not fully understand what it entails. A flange is a critical component used to connect pipes, valves, pumps, and other equipment, forming a robust, leak-proof joint. The American Standard flanges are designed in accordance with specific standards set forth by the American
The Role of Threaded Flanges in Enhancing Pipeline Integrity
The Role of Threaded Flanges in Enhancing Pipeline Integrity Table of Contents Introduction to Threaded Flanges What Are Threaded Flanges? The Importance of Threaded Flanges in Pipeline Systems Applications of Threaded Flanges Advantages of Using Threaded Flanges Design and Manufacturing of Threaded Flanges Installation and Maintenance Best Practices Frequently Ask
Understanding Flanged Connections: Essential Insights for Your Construction Projects
Flanged connections are vital components in various piping systems, especially in the construction and decorative materials sector. They play a critical role in ensuring the integrity and stability of piping connections, making them an essential consideration for engineers, architects, and builders alike. At its core, a flanged connection consists of two flat surfaces with matching holes, typicall
Durable Flanged Connection from China Manufacturers Enhances Pipeline Reliability
In refinery turnarounds and plant shutdowns, durable flanged connection from China manufacturers demonstrates its practical advantages. The ability to quickly disassemble and reassemble piping sections helps maintenance teams meet tight schedule windows, minimizing production losses during critical servicing periods.
Durable Axle-Type Forgings for Machinery from China Manufacturers Enhance Equipment Longevity
For OEMs seeking to improve equipment reliability, durable axle-type forgings for machinery from China manufacturers offer a proven solution. Their balanced combination of mechanical properties and production consistency makes them a practical choice for critical drivetrain components.